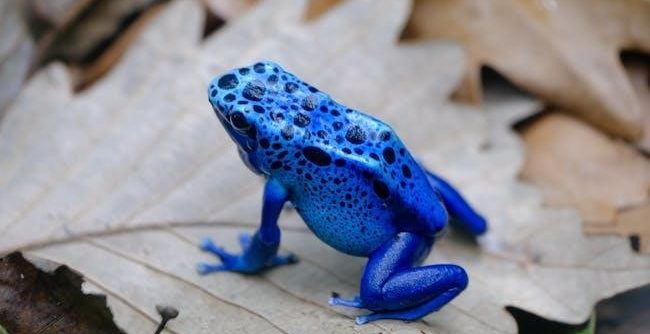
The AWS D17.1/D17.1M:2024 standard outlines fusion welding requirements for aerospace applications‚ ensuring safety and reliability in aircraft and space hardware. It covers design‚ qualification‚ and inspection processes‚ providing updated guidelines for welders and procedures to meet modern aerospace demands.
Overview of the Standard
The AWS D17.1/D17.1M:2024 standard is a comprehensive document outlining requirements for fusion welding and non-destructive examination (NDE) in aerospace applications. It applies to both flight and non-flight hardware‚ ensuring structural integrity and safety. The specification covers welding processes such as electric arc and high-energy beam welding‚ as well as materials like aluminum‚ nickel‚ and cobalt alloys. It emphasizes personnel qualification‚ procedure development‚ and inspection criteria. Conformance to this standard is critical for compliance with aerospace industry regulations and contract requirements‚ making it a cornerstone for quality assurance in aerospace welding practices.
Scope and Application
The AWS D17.1/D17.1M:2024 standard applies to fusion welding of aerospace hardware‚ covering both flight-critical and non-flight components. Its scope includes electric arc and high-energy beam welding processes. The standard addresses design requirements‚ personnel certification‚ and non-destructive testing methods. It is essential for ensuring compliance with federal aviation regulations and industry standards. Proper application of this standard guarantees the reliability and safety of welded aerospace components‚ making it a critical reference for manufacturers and engineers in the aviation and space industries.
Key Changes in the 2024 Edition
The 2024 edition introduces updated NDE methods‚ revised acceptance criteria‚ and enhanced process controls. It aligns with latest FAA regulations‚ improving safety and compliance in aerospace welding practices.
Major Revisions and Updates
The AWS D17.1/D17.1M:2024 edition incorporates significant revisions‚ including enhanced non-destructive examination (NDE) techniques and updated acceptance criteria for weld quality. New sections address advanced materials and emerging welding technologies. The standard also strengthens process control measures‚ ensuring consistency and reliability in aerospace applications. Additionally‚ it aligns with the latest Federal Aviation Administration (FAA) regulations‚ emphasizing safety and compliance in the production and maintenance of flight hardware. These updates reflect the evolving needs of the aerospace industry‚ focusing on improved quality and performance.
Impact on Aerospace Welding Practices
The AWS D17.1/D17.1M:2024 standard significantly influences aerospace welding practices by introducing updated guidelines for fusion welding and non-destructive examination (NDE). It enhances process consistency‚ ensuring higher-quality welds for flight and non-flight hardware. The revised acceptance criteria and inspection methods improve defect detection and reduce variability. These changes promote adherence to strict safety standards‚ optimizing welding outcomes for critical aerospace components. By aligning with advanced technologies and materials‚ the standard supports innovation while maintaining rigorous quality control‚ benefiting both manufacturers and regulatory bodies in the industry.
Compliance and Certification
The AWS D17.1/D17.1M:2024 is an American National Standard approved by ANSI‚ requiring conformance to all provisions when specified in contract documents for aerospace applications.
FAA Regulations and Requirements
Compliance with FAA regulations is mandatory for welding processes involving aircraft‚ rotorcraft‚ and engines. The AWS D17.1/D17.1M:2024 standard requires the Engineering Authority to perform design analyses and implement process controls. When welding is applied to FAA-regulated components‚ adherence to the standard’s provisions is critical. The specification ensures that all welding activities meet federal aviation standards‚ maintaining safety and reliability in aerospace applications. This includes strict process monitoring and documentation to comply with regulatory demands.
Conformance to the Specification
Conformance to AWS D17.1/D17.1M:2024 is mandatory when the specification is cited in contract documents. All provisions must be followed unless explicitly exempted. Non-compliance can lead to critical safety risks‚ making adherence essential for aerospace applications. The standard ensures consistency and quality in welding processes‚ materials‚ and inspections. Deviations must be clearly documented and approved. Strict compliance guarantees that welded components meet the required performance and safety standards for flight hardware‚ ensuring reliability and durability in aerospace systems. Proper documentation and traceability are also required to verify conformance. This ensures accountability and integrity in all aerospace welding projects. Compliance with the specification is non-negotiable for maintaining the highest industry standards and regulatory requirements. By adhering to these guidelines‚ manufacturers can ensure their products meet the rigorous demands of the aerospace industry. Conformance is verified through rigorous testing‚ inspection‚ and documentation‚ ensuring that all welding processes align with the specification’s requirements. This level of compliance is critical for achieving the safety and performance expectations of aerospace applications. Through strict adherence‚ the standard helps prevent defects and ensures the longevity of welded components in demanding environments.
Non-Destructive Examination (NDE)
AWS D17.1/D17.1M:2024 emphasizes NDE for verifying weld quality without damaging components. Techniques like radiography (RT)‚ ultrasonic testing (UT)‚ magnetic particle testing (MT)‚ and penetrant testing (PT) are specified to ensure aerospace weld integrity and compliance with safety standards.
Methods and Techniques
AWS D17.1/D17.1M:2024 specifies non-destructive examination (NDE) methods for aerospace welding‚ including radiography (RT)‚ ultrasonic testing (UT)‚ magnetic particle testing (MT)‚ and liquid penetrant testing (PT). These techniques are used to detect surface and internal defects in welds‚ ensuring compliance with stringent aerospace safety standards. The standard provides detailed procedures for each method‚ emphasizing proper equipment calibration‚ test sensitivity‚ and interpretation criteria to maintain high-quality weld inspection and reliability in flight hardware applications.
Acceptance Criteria
AWS D17.1/D17.1M:2024 establishes clear acceptance criteria for welds in aerospace applications‚ focusing on defect limits‚ surface finish‚ and mechanical properties. The standard specifies allowable imperfections based on hardware classification‚ with stricter requirements for flight hardware. Criteria include maximum porosity levels‚ lack of fusion thresholds‚ and acceptable surface roughness. Visual‚ dimensional‚ and NDE results must comply with these guidelines to ensure weld integrity and reliability‚ guaranteeing aerospace components meet safety and performance standards. Documentation of acceptance criteria is mandatory for traceability and verification purposes.
Personnel and Procedure Qualification
AWS D17.1/D17.1M:2024 requires welders and operators to meet specific qualification criteria through testing and documentation. Procedures must be validated to ensure compliance with aerospace welding standards. Welder qualification involves demonstrating competence in fusion welding processes‚ while procedure qualification ensures that welding parameters and techniques meet specified requirements. Detailed records of qualifications and testing are essential for traceability and compliance‚ ensuring consistency and reliability in aerospace welding practices. This section emphasizes the importance of proper training‚ certification‚ and documentation to maintain high-quality welds in critical applications.
Welder and Operator Requirements
Welders and operators must meet stringent qualification criteria under AWS D17.1/D17.1M:2024. They are required to pass performance qualification tests to demonstrate proficiency in fusion welding processes. The standard specifies that welders must be certified for specific materials and thickness ranges‚ ensuring competence in aerospace applications. Operators are also mandated to undergo training and testing to operate advanced welding equipment effectively. The number of allowable rework attempts is restricted‚ and all qualifications must be documented for traceability. This ensures that all personnel involved in aerospace welding meet the highest standards of skill and reliability.
Procedure Qualification and Records
Procedure qualification records (PQRs) are essential for validating welding procedures under AWS D17.1/D17.1M:2024. Each PQR must detail the welding parameters‚ materials‚ and test results to ensure compliance with the standard. Welding procedure specifications (WPS) are derived from these records‚ providing clear instructions for welders. The standard mandates that all PQRs and WPS must be approved by designated authorities and maintained for traceability. Additionally‚ records must include mechanical test results and NDE outcomes‚ ensuring that all procedures meet stringent aerospace requirements. Non-compliance can result in certification loss‚ emphasizing the critical importance of accurate documentation.
Materials and Applications
AWS D17.1/D17.1M:2024 covers fusion welding for various aerospace alloys‚ including aluminum‚ titanium‚ and steel‚ providing guidelines for their application in aircraft‚ spacecraft‚ and engine components.
Alloys and Metals Covered
The AWS D17.1/D17.1M:2024 standard addresses fusion welding requirements for a variety of alloys and metals commonly used in aerospace applications. These include aluminum alloys‚ titanium‚ nickel-based alloys‚ cobalt alloys‚ magnesium alloys‚ and steel. Each material has specific properties that make it suitable for different aerospace components‚ such as high strength-to-weight ratios‚ corrosion resistance‚ and thermal stability. The standard provides detailed guidelines for welding these materials to ensure structural integrity and performance in demanding environments.
Application Areas in Aerospace
AWS D17.1/D17.1M:2024 is pivotal in aerospace welding‚ covering both flight and non-flight hardware. It applies to aircraft structures‚ engine components‚ and spacecraft systems‚ ensuring weld quality and reliability. This standard is essential for manufacturing and repairing critical aerospace parts‚ maintaining safety and performance under extreme conditions. Its guidelines are integral to meeting stringent industry and regulatory demands‚ making it a cornerstone for modern aerospace welding practices.
Documentation and Record-Keeping
AWS D17.1/D17.1M:2024 requires detailed documentation for welder qualification‚ procedure records‚ and inspection results. Accurate records ensure compliance with specifications and facilitate traceability for aerospace applications.
Required Documentation
The AWS D17.1/D17.1M:2024 standard mandates specific documentation‚ including welding procedure specifications (WPS)‚ procedure qualification records (PQR)‚ and welder performance qualification (WPQ) records. These documents ensure compliance with aerospace welding standards. Additionally‚ non-destructive examination (NDE) reports and material certification records must be maintained. Accurate and complete documentation is critical for traceability‚ quality control‚ and regulatory compliance. Failure to maintain proper records can result in non-compliance and potential rejection of aerospace components‚ emphasizing the importance of meticulous record-keeping practices.
Importance of Accurate Records
Accurate records are crucial for ensuring compliance‚ traceability‚ and quality control in aerospace welding. They provide a detailed history of welding processes‚ materials‚ and inspections‚ enabling verification of compliance with AWS D17.1/D17.1M:2024. Precise documentation supports regulatory audits and maintains accountability. Inaccurate or incomplete records can lead to component rejection‚ safety risks‚ and legal issues. Therefore‚ maintaining accurate and accessible records is essential for upholding the integrity and reliability of aerospace welding operations‚ ensuring adherence to strict industry standards.
Quality Control Measures
AWS D17.1/D17.1M:2024 emphasizes rigorous quality control through process monitoring‚ inspection‚ and testing to ensure adherence to aerospace welding standards‚ maintaining safety and reliability in critical applications.
Process Control and Monitoring
AWS D17.1/D17.1M:2024 emphasizes strict process control and monitoring to ensure high-quality aerospace welding. It outlines requirements for real-time oversight of welding operations‚ including parameter verification and documentation. The standard mandates detailed record-keeping‚ such as welder performance qualifications and procedure validation. Regular inspections and testing are required to verify compliance with specified criteria. Advanced monitoring techniques‚ like automated data acquisition‚ are recommended to maintain consistency and traceability. These measures ensure adherence to FAA regulations and industry standards‚ guaranteeing the integrity of aerospace components. Proper documentation and traceability are critical for audit and compliance purposes.
Inspection and Testing
AWS D17.1/D17.1M:2024 requires rigorous inspection and testing protocols for aerospace welds‚ ensuring compliance with strict quality standards. Non-destructive examination (NDE) methods‚ such as radiography and ultrasonic testing‚ are mandated to detect defects. Visual inspections and mechanical tests‚ like tensile and bending‚ validate weld integrity. Specific acceptance criteria are outlined for different alloys and applications‚ ensuring reliability. Documentation of inspection results is critical for traceability and compliance with FAA regulations. These measures guarantee the safety and performance of aerospace components‚ aligning with industry best practices and standards. Precise testing ensures adherence to specified requirements‚ maintaining the highest quality in aerospace welding.
Aerospace Applications
AWS D17.1/D17.1M:2024 governs fusion welding for aircraft‚ space hardware‚ and related systems. It addresses flight-critical components‚ ensuring high-strength‚ lightweight welds for aluminum‚ titanium‚ and other alloys‚ meeting aerospace demands.
Flight Hardware Welding
AWS D17.1/D17.1M:2024 provides critical guidelines for welding aerospace flight hardware‚ ensuring structural integrity and safety. It specifies requirements for fusion welding processes‚ including arc and beam welding‚ for materials like aluminum‚ titanium‚ and high-strength alloys. The standard emphasizes strict process control‚ non-destructive examination (NDE)‚ and documentation to verify weld quality. Compliance with these requirements is essential for maintaining the reliability and performance of aircraft and space systems in service.
Non-Flight Hardware Welding
AWS D17.1/D17.1M:2024 also addresses welding requirements for non-flight hardware‚ such as ground support equipment and tooling. While less stringent than flight hardware standards‚ it ensures weld quality and reliability. The specification covers fusion welding processes‚ materials‚ and NDE methods for non-flight components‚ providing guidelines to maintain structural integrity and performance. These requirements support the overall safety and efficiency of aerospace operations‚ even for non-critical hardware.
Procurement and Availability
The AWS D17.1/D17.1M:2024 standard can be purchased in PDF or hardcopy format through the American Welding Society’s official store or authorized distributors‚ with pricing varying for members and non-members.
How to Purchase the Standard
The AWS D17.1/D17.1M:2024 standard is available for purchase through the American Welding Society’s official store or authorized distributors. It can be obtained in both PDF and hardcopy formats. Members of AWS receive discounted pricing‚ with the PDF version costing $174.00 and the hardcopy available at a slightly higher rate. Non-members can purchase the standard for $232.00. Payments can be made securely online‚ and the PDF version is immediately downloadable upon completion of the transaction. Ensure to purchase from authorized sources to guarantee authenticity and access to the most current edition.
Availability in PDF and Hardcopy
AWS D17.1/D17.1M:2024 is available in both PDF and hardcopy formats for flexibility and accessibility. The PDF version is suitable for digital access and can be downloaded immediately after purchase‚ while the hardcopy provides a physical reference. Both formats are distributed by the American Welding Society (AWS) and authorized resellers‚ ensuring authenticity and up-to-date content. The PDF is priced at $174.00 for AWS members and $232.00 for non-members‚ with the hardcopy available at a slightly higher cost. Purchasing from official sources guarantees compliance with the latest standards.
Future Trends and Updates
AWS D17.1/D17.1M:2024 reflects advancements in welding technology‚ with ongoing updates addressing emerging technologies and industry needs. Regular revisions ensure alignment with aerospace innovation and regulatory changes.
Emerging Technologies
The AWS D17.1/D17.1M:2024 standard incorporates advancements in fusion welding technologies‚ including laser beam welding and electron beam welding‚ enhancing precision and efficiency in aerospace applications. These innovations address the growing demand for lightweight‚ high-strength materials in aircraft and space systems. The updated standard also emphasizes the integration of automation and robotics‚ enabling faster production cycles while maintaining stringent quality standards. These emerging technologies ensure the aerospace industry remains at the forefront of manufacturing excellence and safety.
Industry Collaboration and Development
The AWS D17.1/D17.1M:2024 standard is developed through collaboration between industry experts‚ manufacturers‚ and regulatory bodies‚ ensuring it meets the evolving needs of the aerospace sector. This cooperative effort fosters innovation and standardization‚ promoting consistent quality across the industry. The standard’s updates reflect contributions from leading organizations and professionals‚ aligning with global aerospace manufacturing practices. Such collaboration ensures the specification remains relevant and effective‚ supporting advancements in welding technologies and applications.